リニアステッピングモータは、ステッピングモータの一種であり、直線的な運動を実現するために使用されるモーターです。リニアステッピングモータが自動化技術にもたらす革新的な要素について、以下にいくつかのポイントを挙げてみます:
1. 高精度な位置制御:
- リニアステッピングモータは、微細なステップ単位での位置制御が可能です。この高い精度により、自動化システムにおいて精密な位置決めや移動が実現され、生産効率が向上します。
2. スムーズで静音な動作:
- リニアステッピングモータは、ステッピングモータの特性を活かしたスムーズで静音な動作を実現します。この特性により、機械の動作時の振動や騒音を低減し、快適な作業環境を提供します。
3. 簡易な制御システム:
- ステッピングモータは、パルス制御によって位置を制御するため、比較的単純な制御システムで動作させることができます。このため、制御システムの設計や運用が容易になります。
4. 高速で効率的な動作:
- リニアステッピングモータは高速での動作が可能であり、効率的な生産ラインや自動化システムにおいて、素早い位置変更や移動を実現します。
5. 柔軟な適用範囲:
- リニアステッピングモータは、様々な産業分野や自動化技術に適用可能です。精密機器の位置調整から製造ラインの自動化まで幅広い用途で活用されています。
リニアステッピングモータは、高い精度や静音性、効率的な動作などの特性により、自動化技術における革新をもたらしています。これらの特徴を活かして、生産性向上や品質管理の向上、効率的な生産ラインの構築など、様々な分野で革新的なソリューションを提供しています。
PR
ステッピングモータエンコーダの位置ズレを補正する方法は、エンコーダの正確な位置検出を確保し、制御システムとの整合性を維持するために重要です。以下に、ステッピングモータエンコーダの位置ズレを補正する一般的な方法をいくつか示します:
ソフトウェアによる補正:
1. ソフトウェア補正:
- 制御システムのソフトウェアを使用して、エンコーダの位置ズレを補正することができます。エンコーダの実際の位置とシステムが認識する位置とのずれを修正するアルゴリズムを実装します。
2. フィードバック制御:
- フィードバック制御を使用して、エンコーダのフィードバック情報を元にモーターの位置をリアルタイムで調整し、ズレを補正します。
機械的な調整:
1. エンコーダの取り付け位置調整:
- エンコーダの取り付け位置を調整して、モーターシャフトとエンコーダーシャフトの位置合わせを正確に行います。正確な取り付け位置を確保することで、位置ズレを最小限に抑えます。
2. エンコーダの位置調整:
- エンコーダ本体の位置を微調整して、正確な位置検出が可能になるようにします。適切な工具を使用して、エンコーダの位置を調整します。
パラメータ設定と再調整:
1. エンコーダパラメータの設定:
- 制御システムのパラメータを適切に設定して、エンコーダの解像度やカウント数などを正確に反映させます。
2. 再調整とテスト:
- エンコーダの位置ズレを補正した後、再度システムをテストして正確な位置検出が行われていることを確認します。必要に応じて再調整を行います。
ステッピングモータエンコーダの位置ズレを補正する際には、ソフトウェアや機械的な調整を組み合わせて正確な位置検出を確保することが重要です。ズレを最小限に抑えることで、システムの制御精度を向上させることができます。
ノイズ対策とEMC(Electromagnetic Compatibility)設計におけるスイッチング電源の注意点について説明します。
スイッチング電源のノイズ対策とEMC設計の注意点:
1. フィルタリング:
- スイッチング電源から発生するノイズを抑えるために、入力側や出力側に適切なフィルタ回路を設計します。コモンモードフィルタや差動モードフィルタを使用して、ノイズの除去を行います。
2. 適切なグランディング:
- スイッチング電源内の各部品やケーブルを適切に接地することで、ノイズの発生や伝播を抑えます。グランディングの設計に注意し、地線を効果的に配置して地絡を防ぎます。
3. 過渡対策:
- スイッチング動作に伴う急激な電圧変化やスパイクを抑えるために、過渡対策を行います。適切な過渡抑制回路やサージ吸収ダイオードを使用して、電源ラインの安定性を確保します。
4. シールド化:
- スイッチング電源や周辺回路をEMI(Electromagnetic Interference)から保護するために、シールド化を行います。適切なシールドケースやシールド材料を使用して、外部からの電磁波の影響を軽減します。
5. 適切な配置:
- スイッチング電源や周辺部品の配置に注意し、ノイズの影響を最小限に抑えます。ノイズ源や感受性の高い部品との距離を適切に設定し、クロストークやノイズの影響を軽減します。
6. EMC規格への準拠:
- EMC規格に準拠するために、適切なテストや評価を行います。設計段階からEMCを考慮し、適合性テストを通過するための対策を講じます。
これらの注意点を考慮してスイッチング電源の設計を行うことで、ノイズの問題を最小限に抑え、EMC規格への適合性を確保することができます。結果として、信頼性の高い動作と周囲機器への影響を最小限に抑えた設計が可能となります。
バイポーラステッピングモータは、精密な位置制御が必要な医療機器において広く応用されています。以下に、バイポーラステッピングモータが医療機器において利用される具体的な事例をいくつか紹介します:
応用事例:
1. CTスキャナー:
- CT(Computed Tomography)スキャナーにおいて、バイポーラステッピングモータはX線源や患者テーブルの位置制御に使用されます。高い精度と安定性を持つバイポーラステッピングモータは、画像の品質向上とスキャンの速度改善に貢献します。
2. MRI機器:
- MRI(Magnetic Resonance Imaging)機器においても、バイポーラステッピングモータは患者の位置調整や機器の部品移動などに使用されます。MRI検査においては、信頼性や静音性が求められるため、バイポーラステッピングモータが適しています。
3. 医療用ロボット:
- 医療用ロボットにおいて、手術支援やリハビリテーションなどの用途にバイポーラステッピングモータが活用されています。手術ロボットの精密な動作やリハビリテーション機器の運動制御において重要な役割を果たします。
4. 薬剤デリバリーシステム:
- バイポーラステッピングモータは、薬剤の正確な投与量や流速を制御するための薬剤デリバリーシステムにも使用されています。薬物の精密な供給を可能にし、治療の効果を向上させます。
5. 人工呼吸装置:
- バイポーラステッピングモータは、人工呼吸装置などの医療機器において、呼吸のリズムや深さを制御するために使用されます。安定した動作と精密な制御が要求される場面で活躍します。
バイポーラステッピングモータは、医療機器において精密な位置制御や動作が必要とされる多くの用途で利用されています。その高い制御性能や信頼性により、医療現場において安全かつ効果的な機能を提供しています。
バイポーラステッピングモータのマイクロステップ駆動技術は、ステッピングモータを通常のステップよりも細かいステップに分割して制御する技術です。これにより、ステッピングモータの角度分解能を向上させ、滑らかで精密なモーション制御を実現することができます。
以下はバイポーラステッピングモータのマイクロステップ駆動技術に関する詳細です:
1. ステップ分解能の向上:
- 通常のステッピングモータは1.8度(200ステップ)や0.9度(400ステップ)などの角度で回転しますが、マイクロステップ駆動技術を使用すると、これをさらに細かいステップに分割することが可能です。例えば、1/4ステップや1/8ステップ、1/16ステップなど、より多くのステップ数で角度を分割できます。
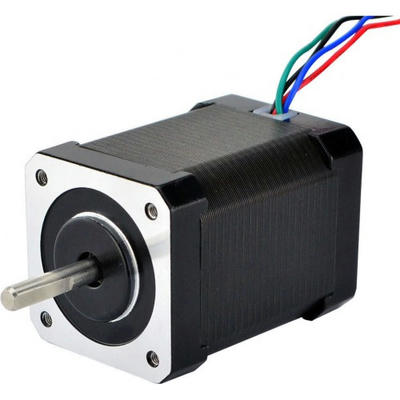
「写真の由来:Nema 17 バイポーラステッピングモータ 1.8°65Ncm (92oz.in) 2.1A 3.36V 42x42x60mm 4 ワイヤー」
「写真の由来:Nema 17 バイポーラステッピングモータ 1.8°65Ncm (92oz.in) 2.1A 3.36V 42x42x60mm 4 ワイヤー」
2. 滑らかな動作と低振動:
- マイクロステップ駆動技術を使用すると、ステッピングモータがより細かいステップで動作するため、モーターの回転が滑らかになります。これにより、振動や騒音を低減し、より静かで安定した動作を実現することができます。
3. 精密な位置制御:
- マイクロステップ駆動技術を使用することで、ステッピングモータの位置制御が向上します。細かいステップでの動作により、より精密な位置決めや微調整が可能となります。
4. トルク特性の改善:
- マイクロステップ駆動技術により、ステッピングモータのトルク特性も改善されます。特に低速域でのトルクが向上し、微小な動作や停止時の位置保持などにおいて効果を発揮します。
バイポーラステッピングモータのマイクロステップ駆動技術は、精密なモーション制御を必要とするアプリケーションや装置において、精度や効率を向上させるために広く利用されています。
プロフィール
HN:
No Name Ninja
性別:
非公開
最新記事
(07/30)
(07/24)
(07/18)
(07/11)
(07/05)